Applications and uses
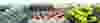
D37 to D75 Series
Pressure: 7 to 10 bar
Flow: 6 to 12.7m3/min
37 to 75kW
Air and water-cooled, fixed and regulated speed, silicone free and ISO-8573 Class Zero (2010) certified oil-free compressors
DX90 (RS) to DX160 (RS)
Pressure: 4 to 10.5 bar
Flow: 6.7 to 28.3m3/min
90 to 160kW
Two-stage, oil-free screw compressors, fixed or regulated speed, silicone free and ISO-8573 Class Zero (2010) certified oil-free screw compressors
D15H (RS) to D37H
Pressure: 5 to 10 bar
Flow: 0.32 to 5.86m3/min
15 to 37kW
Single-stage, oil-free water-injected screw compressors, fixed or regulated speed, silicone free and ISO-8573 Class Zero (2010) certified oil-free screw compressors
When it comes to food safety, health and safety is extremely important. There are rigorous processes in place to ensure that the food we eat is safe, healthy and tasty! Contaminated air could cause product spoilage which is a health risk for the consumer and could cause irreparable damage to a company brand.
Oil free compressors can safely be used for product handling, transportation, food filling machines, air knives for cutting or peeling food products and for vacuum packaging goods as well as many other uses within this diverse sector.
Within the drugs and pharmaceutical industry, quality and safety are strictly adhered to. Any products that reach the market must be rigorously tested to ensure they are safe for consumption. With so many people relying on products from the pharmaceutical industry, clean air is critical for this industry.
Businesses within this sector rely on clean compressed air for a variety of uses including fermentation in antibiotic production, aeration for oxidation processes, tablet production and packaging and bottling of medications.
Toxic chemical and unstable gases will often be part of the process production within the chemical industry. In hazardous processes oil free compressors will help to eliminate the risk of explosions and process disruption.
They will also increase product purity resulting in better processes, less waste and increased safety for those relying on the products. Typical uses of compressed air within the chemical industry include process air, control valves and cylinders, material handling as well as air curtains and product drying.
A lot of work goes into producing fabrics with elegant designs and intricate details. Contaminated air could cause damage to materials resulting in costly repairs and maintenance or worse, product wastage. Oil free compressors are used within the textile industry for intricate tasks such as air-jet weaving and spinning, texturising and pneumatic transport.
Process reliability is essential within the oil and gas industry where hazardous chemicals are often used. Popular uses within this sector include nitrogen generation, buffer air, control/ instrument air and process operations for sulphur removal, catalyst regeneration and process heaters, to name a few.
High quality vehicles rely on high quality compressed air. Impure air can result in damage to a product finish and may even require expensive repair work to fix. Whether compressed air is used for tyre inflation or more complex uses, such as air operated robots, pure air provides the best results. Typical uses within this industry include product finishing with spray paint, pneumatic tools, plasma cutting and welding as well as cleaning.
For smooth running control systems, ultra-clean conditions need to be maintained. Furthermore, where expensive electronic equipment is concerned, there can be no room for error or risk. Compressed air is often used in electronics for actuating valves and tools within control systems as well as moving and placing electrical components. Additional common uses include cleaning PCB boards and in the production of electrical equipment.
A Guide to Benchmarking Performance with ISO8573 1, ISO 12500, and ISO 7183